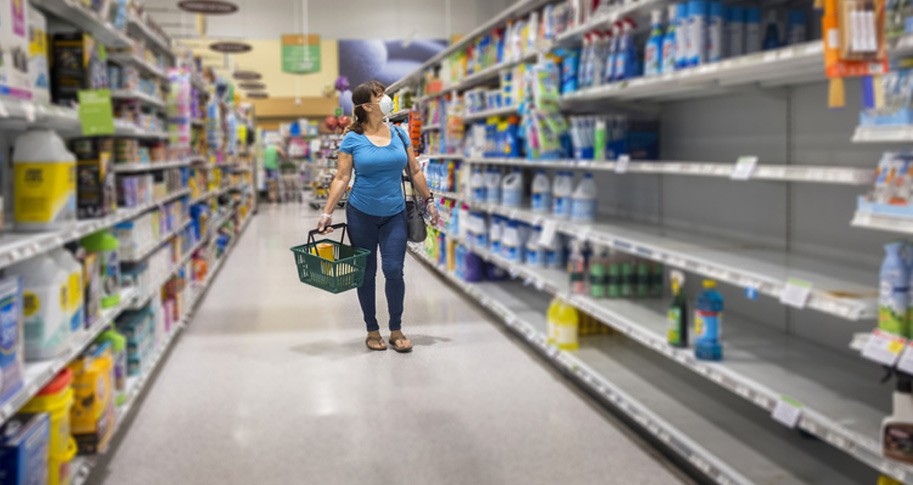
"Nobody gave a rat's [behind] about N95 masks before the pandemic, other than people who were painting, or spraying pesticides, or working in a medical facility." That line from a supply chain executive overlooks a few workers, but it gets the point across.
In April 2020, one source estimated a 1700% demand spike for N95 respirators. Firms carry safety stock to buffer against unexpected demand. But a 1700% increase? It would have been cost prohibitive to carry enough safety stock to meet such an extreme, rare uptick in demand for most any item, including masks with limited shelf lives. The trade-offs would have been too severe.
The White House's recent supply chain resilience report repeatedly encourages firms to increase safety stock and add both manufacturing and supplier capacity to make supply chains more resilient during future disruptions. Those changes are also intended to help companies in certain industries meet projected demand for products like semiconductors, large capacity batteries, and electric vehicles.
Though the report mentions supply, demand, inventory, and capacity, it does little to explain how they are connected or how managing them involves trade-offs.
Before policymakers further incentivize, encourage, or coerce companies to follow the report's recommendations, they should consider the potential trade-offs. Those trade-offs may impact firm performance, stifle innovation, produce unnecessary waste, and limit companies' ability to pursue the Biden administration's environmental and social sustainability goals.
What Creates Supply Chain Uncertainty?
Demand forecasting is a fundamental part of supply chain management for reducing demand uncertainty. Firms use historic demand data, information on current trends, and other factors to plan how much of a given product or raw material to produce, manufacture, or purchase during a set period.
Demand planning for products like sunscreen, pumpkin pie filling, and Christmas ornaments takes seasonality into account. Many foodstuffs and pharmaceuticals see steady year-round demand. Demand for innovative tech products can be more difficult to predict because a lack of historic data requires mangers to lean heavily on market research and intuition.
Modern technology makes it easier than ever for suppliers, manufacturers, transportation firms, and retailers to share information and coordinate demand planning across a supply chain, allowing for more accurate demand forecasts.
However, unpredictable factors can undermine even the most carefully constructed demand forecasts. An item may suddenly go out of style, leaving a retailer with racks of clothing or shelves of obsolete tech products no one will buy at full price.
Consumer tastes may also shift the other way, with something as innocuous as a celebrity's unexpected Twitter endorsement causing a sudden run on a product.
Myriad factors including a retailer's week-long discount of a product, a natural disaster, and a global pandemic can leave firms scrambling to try to meet unexpected demand.
Ideally, firms throughout a supply chain reduce supply uncertainty by sharing information and coordinating when forecasting demand. That transparency gives forecasters accurate information on available supply. After all, there is no point in a smartphone manufacturer planning to make one hundred million phones over a six-month period if its semiconductor suppliers cannot provide enough chips to meet that goal.
A lack of transparency is one factor that can cause supply uncertainty.
Many manufacturers do not know the identities of their suppliers' suppliers, since suppliers often consider that information a "trade secret." In those situations, a manufacturer may get a nasty surprise when they learn that their suppliers of a key part all relied on the same raw material supplier – and that supplier will be off-line for the next month.
Many other factors can cause supply uncertainty, including wars, political unrest, trade wars, worker protests, factory fires, natural disasters, transportation failures, and unexpected global demand spikes for key raw materials.
How Buffers Reduce Uncertainty
Supply chain managers' work involves balancing demand and supply while addressing the inevitable uncertainties as effectively as possible using a few time-tested buffers. It is an ongoing battle that involves managing trade-offs that sometimes disappoint a firm's upper management, accountants, shareholders, customers, or end consumers.
Safety stock is the most common buffer against uncertainty. Excess stock of raw materials, parts, or finished products helps firms navigate unexpected demand spikes or supply shortages.Safety stock levels are calculated using factors like expected demand, forecast error, the amount of time a supplier typically takes to fill an order, and desired service level.
The concept of service level is key to understanding the trade-offs involved with safety stock. It is the likelihood that a firm will be able to fill all customer orders during a given period. A manufacturer with a 99% service level would expect, with a 99% probability, to fill every customer order without running out of inventory and experiencing a stock-out.
Stock-outs can cause customers to take their business elsewhere, so one might assume that every firm in every industry aims for an extremely high service level. But that is not necessarily the case, due to the trade-offs required to achieve such service levels. Using safety stock to raise service levels is a classic case of diminishing returns. That is, it requires many more resources to raise a service level from 95% to 97% than it does to raise a service level from 83% to 85%.
Supply chain managers must weigh the benefits of being able to fulfil as many customer orders as possible against the costs of safety stock. Firms that hold lots of safety stock have to store it somewhere. Depending on the item, there is also a risk that it will spoil or become obsolete, damaging a firm's bottom line and adding unnecessary waste to landfills.
Capacity refers to how much output a firm in a supply chain can produce during a set period. Supply chains typically have some spare capacity to buffer against uncertainty. For instance, a factory that usually runs two eight-hour shifts per day can run a third shift and pay employees overtime when an unexpected demand spike occurs.
There are many ways to add capacity to mitigate risk. A factory may expand its facilities and add new employees and machines. A manufacturer that relies on a single supplier of a key raw material may contract additional suppliers in other regions. Growing companies may add new suppliers, manufacturers, transportation firms, or distributors to keep pace with their growth. Or a firm may contract a backup factory or trucking firm to be prepared to fill in during an emergency.
Firms with too little capacity in their supply chain risk repeatedly disappointing customers and going out of business. But adding capacity is costly, particularly if much of that extra capacity goes unused. Wasted capacity siphons funds that could be spent on innovation, employee benefits, or environmental sustainability. Supply chain managers strive to balance the trade-offs and find a capacity level that buffers against uncertainty without being overly wasteful.
Time is the third buffer against uncertainty. Put simply: the customer can wait.
That idea can be jarring after years of e-commerce sites offering fast, cheap delivery of countless products. Those deliveries created expectations that made the pandemic's shortages more shocking to many consumers than they would have been two decades ago.
The ubiquity of rapid e-commerce deliveries is evidence of the overall effectiveness of modern supply chains. However, unpredictable disruptions sometimes leave supply chain managers no choice but to miss a delivery window to an industry customer or end consumer.
Firms risk losing a customer every time they resort to using the time buffer. So, they rarely do so intentionally.
Conclusion
Given the connections between supply uncertainty, demand uncertainty, and buffers, policymakers should be very judicious in encouraging firms to do things like increasing safety stock or adding capacity. While adding safety stock or capacity may allow companies to meet unexpected spikes in demand due to disruptions, there are trade-offs to consider. Such interventions will add cost to the supply chain, likely hurting firms' financial performance. Adding buffer inventory and capacity may also lead to unnecessary waste and limit companies' ability to invest in sustainability and innovation.
Like supply chain managers, policymakers face a delicate balancing act. They need to consider the advice of those who believe that many of our supply chains need to be fundamentally overhauled.
But they must weigh that responsibility against factors like trade-offs, the potential for government intervention to create negative unintended consequences, and many experts' belief that our supply chains performed remarkably well during the pandemic.