COVID-19: The Wake-Up Call for Supply Chain Management
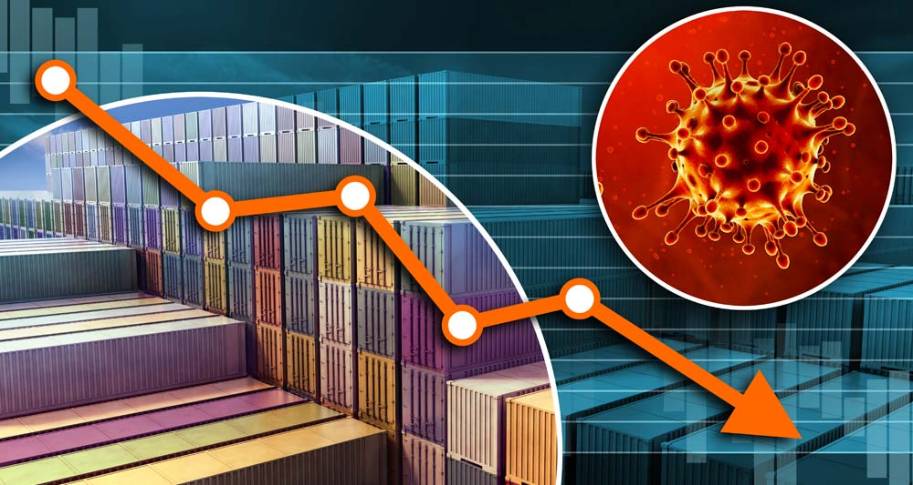
October 16, 2020 | By Ryan Decker
Researcher: Remko Van Hoek
We all remember the panic of mid-March 2020.
Offices shut down, schools closed and everyone went straight to their local Walmart to stock up on … toilet paper. Why was there a worldwide run on toilet paper, of all things? Experts believe that just like the bank runs of the Great Depression, fear drove consumers to stock up before others had the same idea.
Because of COVID-19, hand sanitizer, medical supplies, bottled water and cleaning products quickly flew off the shelves. Retailers and suppliers could not keep up, and items were out of stock for days or even weeks. As a result, supply chain experts called for improved supply chain resilience and the development of supply chain recovery scenarios and approaches.
Even so, many companies were slow to respond. As of March 22, only half of companies surveyed had developed business continuity plans for the COVID-19 crisis, and 64% of companies predicted a return to business as usual within 3-6 months. Despite facing textbook risk scenarios and calls for improved resilience, most companies hoped for a quick return to normalcy.
Even with most factories reopened and operating at full capacity, many companies are still facing significant supply chain disruptions. According to a survey done by the Chartered Institute of Procurement & Supply, it may take a year or more to return to pre-pandemic supply chain levels.
In his impact pathway paper, “Research opportunities for a more resilient post-COVID-19 supply chain – closing the gap between research findings and industry practice,” Remko Van Hoek suggests pathways to improve supply chain resilience. Based on interviews with supply chain executives, Van Hoek explores the practical and social implications of the pandemic in supply chain management.
Closing the Gap Between Research and Practice
At the start of the pandemic, the supply chain industry faced textbook supply and demand risk scenarios, and many in the industry called for resilience and recovery scenario development. Even so, many companies did not have a plan and rather hoped for things to just go back to normal. “This suggests that there is a gap between the understanding of supply chain risks in literature and that in the industry,” Van Hoek states. Supply chain literature has consistently called for more empirical and event-based research – because of the pandemic, those calls can no longer be ignored.
Literature has long warned of the increased risks resulting from globalizing supply chains. To cut costs, companies have reduced the number of suppliers for negotiation leverage and relied on specialized factories for greater economies of scale. In essence, the cost obsession and short-term cost focus in supply chain management is causing many resilience challenges in the industry. Globalization and supplier reduction help to lower costs but also lengthen the logistics pipeline and increase the dependency on distant sources and the likelihood of delays.
The shortage of personal protection equipment (PPE) during the early stages of the pandemic endangered the lives of health workers worldwide. Companies who relied on a few global suppliers were unable to produce the necessary supplies for hospitals. For critical supplies (such as masks and other PPE, hand sanitizer, etc.), research suggests companies place a higher emphasis on ensuring supplies than on cost savings. For non-critical supplies, a more collaborative approach is suggested to prevent dangerous shortages from occurring.
Research highlights the benefits of new technologies such as RFID and blockchain to improve supply chain visibility. These technologies help to combat supply chain risks through active information sharing throughout the supply chain. Companies can more accurately monitor inventory positions and logistics flows.
COVID-19 is a much-needed wake-up call for supply chain management. The pandemic provides opportunities for event-based research to improve future practices. To guide future empirical research, Van Hoek conducted a review of public newsfeeds, participated in online seminars and roundtables, and interviewed supply chain executives. Much has changed since the start of the pandemic, but this paper provides an initial broad exploration of the challenges facing global supply chains.
So, How Did We Get Here? Globalization.
Because of the pandemic, lead times extended from days to weeks to months as companies waited for products from foreign suppliers, demand fluctuated wildly between different products, and financial pressure affected relationships between companies and suppliers. Upon speaking with supply chain executives, Van Hoek found that many of the industry perspectives overlap with literature insights.
Supply chain executives reported several different types of disruptions: plant closures, long shipping pipelines and logistical bottlenecks caused complex problems. Factories in China closed during February to try to contain the novel coronavirus. Even when these factories reopened in March, it took time to ramp production back up to normal levels. Ships can also take a month or more to cross the Pacific Ocean, adding to the delay. Many companies turned to air freight instead – causing some airlines to repurpose their passenger planes to increase cargo space.
These disruptions caught supply chain executives off guard. A supply chain vice president of a consumer products company shared that, “We have never been through this level of complexity and no historical data is relevant at this point. We were not prepared to be able to manage supply as you would have hoped we would be.”
Scholars suggest companies avoid overreliance on just a few factories for supplies. It is important to have multiple and flexible sources in case of plant closures or unforeseen issues. While globalization reduces costs, it comes at a price – especially during a pandemic. Many companies began rebalancing their supply-lines to include more near and local sourcing to mitigate supply risks.
“Interestingly enough,” Van Hoek writes, “the tariffs on product from China may have driven a degree of readiness that otherwise may not have been in place.” Many companies diversified their supply base by relying on suppliers outside of China. For one company, this shift proved invaluable during the pandemic. “By the time India and Malaysia went into shutdowns, Chinese suppliers were back up and running so we could shift orders back to China,” a procurement director said.
Similarly, Nike shifted some production to nearshore factories such as Latin America for the U.S. market and Turkey for the EU market. This strategy has many benefits, such as a faster response to consumer demand, more frequent product introductions and improved flexibility during times of crisis.
Riding the Rollercoaster of Demand
If you wanted to social distance in a Walmart or Target during March or April in 2020, shopping in the apparel section was generally a safe bet. March demand for apparel and accessories fell by 20% while demand for food and beverage and essentials grew by 50% according to a Target supply chain vice president. These wild fluctuations make it difficult to know how much inventory to replenish. Companies must determine if demand will stay at these new levels or if it is a temporary outcome of panic buying.
These demand fluctuations are a perfect example of the bullwhip effect, a supply chain phenomenon caused by increasing swings in demand. A small increase in consumer demand can cause a much larger increase in demand further up the supply chain, decreasing supply chain efficiency. Although less efficient, this may actually boost the economy in the short run.
Similarly, the airlines that modified their passenger planes to satisfy the spike in air freight demand saw a decrease in this demand almost immediately. Then with a surplus of cargo planes, airlines had to lower rates to remain competitive. Freightwaves, a transportation market intelligence firm, reported a large spike in outbound transportation in the first half of March, followed by a leveling-off by March 28.
Many companies also saw massive growth in e-commerce due to consumer preference. Walmart’s second quarter net e-commerce sales surged by 97% in the U.S. and 104% in China. Changing shopper behavior brings new demand risks as well. Companies like Walmart have had to quickly adapt to accommodate new ways of shopping.
Necessity Is Still the Mother of Invention
With so much rapid change, companies must move faster than they have in the past. Companies are introducing temperature-taking robots, contactless self-check-out and other solutions because they simply had to do so in order to remain operational. Digitization and automation initiatives have accelerated and have improved visibility. As more companies embrace digitization and active information sharing throughout the supply chain, they can react more efficiently to spikes in demand.
An operations director from Alpargatas, a South American textile company, saw a need to “step up our investment in technology and logistics control towers to get better information and transparency across the supply chain and our supply chain basis, so that we can respond better to demand fluctuations.” Other companies have already seen the benefits of improved supply chain visibility. Nike deployed RFID in its supply chain to track demand and product availability in almost real time, and Maersk uses blockchain to improve the sharing of shipping documents.
These strategies help to reduce the bullwhip effect by shifting capacity in response to demand fluctuations. “While participating supply chain executives do report some investment in additional inventory,” Van Hoek writes, “agility does not have to come at a(n) [higher] inventory cost, nor does a focus on lean mean a focus on cutting inventories for [the] sake of cost reduction.” Investment in new technology to improve supply chain visibility reduces inventory costs while improving agility.
How Can Supply Chains Increase Resilience? Relationships.
In his interviews with supply chain professionals, Van Hoek saw that a focus on relationships with suppliers is key. Companies had to call upon suppliers to get rush deliveries of PPE or renegotiate contracts due to changes in demand. In his interviews with supply chain executives, Van Hoek encountered two different perspectives. Some companies focused on building relationships at the expense of lower prices, while others renegotiated with suppliers and canceled orders due to changes in demand.
Van Hoek warns against taking advantage of the weakened supply market and recommends to instead work collaboratively with specific suppliers. Doing so will make sure critical supplies are received on time. Some companies hope the relationships they strengthen during this crisis will pay off long-term, while others seek shorter-term solutions to combat substantial declines in revenue.
“[Companies] are managing bottlenecks with suppliers carefully and they are using relationship-centric approaches with important suppliers, as is recommended in literature,” Van Hoek writes. Some companies have sacrificed capturing the lowest price from their suppliers to focus on building relationships. Others cut prices to combat lost revenue.
“Some CFOs have unilaterally pushed out payment terms with suppliers,” a CPO of a financial services company states. This action may put relationships at risk and cause lasting damage. In general, a relationship-centric approach is suggested for critical suppliers, and negotiations should only be made with select suppliers – not unilaterally.
What’s Next?
“Those who do not learn from history are doomed to repeat it.” – George Santayana
COVID-19 has provided a rare opportunity for researchers to engage in targeted, event-based research on supply chain resilience and better bridge the gap between literature and industry practice. This research has the potential to impact supply chain decision-making and redesign in ways that earlier, more conceptual research cannot. Closing the gap improves preparedness and contributes to the de-risking of supply chains.
Supply chain management has played a critical role in the pandemic, coordinating shipments of life-saving PPE and medical devices to hospitals around the world – but not without complications. Improving the resilience of these supply chains by closing the gap between literature and practice will help us greatly when the next crisis comes around.