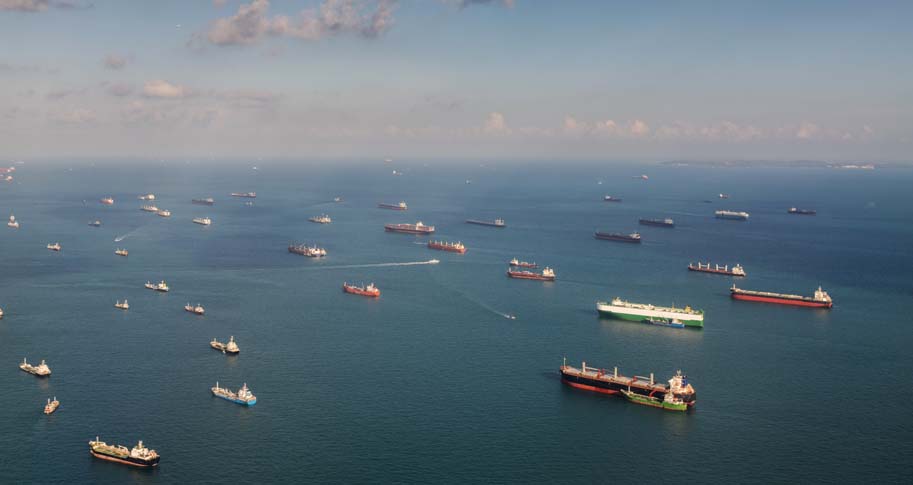
Nearly two years after shortages of goods ranging from toilet paper to N95 masks raised awareness that supply chains exist (and can be disrupted), many are likely wondering why supply chain problems are still ongoing. Indeed, some experts believe that the port congestion we are currently experiencing will take several more months to clear out.
Unfortunately, we cannot tell you that those experts are wrong. What we can do is share a few foundational concepts from supply chain management that will help you better understand the port problem. To do so, we draw from a mathematical modeling technique called system dynamics. System dynamics modeling has helped people understand baffling problems in areas ranging from public housing to farming, but it began as a way to understand the complexities of supply chains.
What the Origins of System Dynamics Can Teach Us about Port Congestion
In the late 1950s, General Electric managers asked MIT’s Jay Forrester why their household appliance factories experienced such drastic swings in demand. They could not keep up with all the orders they received some months. Other times, they received so few orders that they considered laying off half their workers. The traditional view was that the fluctuations stemmed from the natural course of the business cycle, but Forrester was dissatisfied with that fatalistic explanation.
Forrester — a pioneer in computer engineering — created a model depicting how GE’s management policies influenced production, employment, inventories, and backlogs. The model showed that even if consumer demand remained steady, GE’s massive network of wholesalers and distributors would cause problems. Retailers tended to place unnecessarily large orders because they feared they may run out of stock before their orders made their way through GE’s network of wholesalers and distributors. The wholesalers and distributors took those inflated orders at face value and, erring on the side of caution, ordered even more appliances. Those seemingly small decisions added up to big problems for General Electric.
Forrester’s system dynamics perspective has helped many understand the supply chain phenomenon of order variance amplification, widely known as the bullwhip effect. When multiple actors interact in a system with limited information and time-delayed feedback loops, even the most rational decisions by inventory managers can trigger disruptions. And since supply chains are never operated by fully rational decision makers, many other factors can also contribute to the bullwhip effect.
The bullwhip effect provides a useful lens for viewing the current port situation. Like General Electric’s factories, our ports are part of a complex network where otherwise minor factors can add up to big problems.
Consider a stylized example of a maritime supply chain. It starts with container ships approaching the port. Are these ships uniformly distributed, or clustered into groups? A cluster of incoming ships presents the first potential challenge. While a port might be able to process 20 ships a week when spaced out over seven days, unloading will be less efficient if the ships all show up at once. Anchorages must be found, docking priorities decided, and unloading schedules harmonized. Moreover, while ships are anchored outside ports — serving as warehouses instead of transportation — they are not delivering goods. So, shipments become backlogged upstream at the port of export, causing a feedback loop that exacerbates the clustering.
On shore, containers are offloaded by longshoremen, stored temporarily at the port, hauled short distances by dray carriers, stored in nearby warehouses, and then transported to downstream distribution centers by rail or long-haul truck. Each of these nodes represents a potential choke point, with cascading consequences upstream and downstream. For instance, a temporary disruption in drayage carriers can cause containers to collect at the port, leaving no place to unload and worsening port congestion. Drayage can be further slowed by a lack of container chassis if the existing chassis are all sitting under containers waiting to be towed away. Meanwhile, downstream warehouses may detain long-haul truckers for longer periods as they wait to assemble shipments from the delayed containers. This reduces the efficiency of long-haul trucking, diminishing truckers’ ability to clear the port of containers or transfer goods between distribution centers.
Notably, the configuration dependent properties of this system can result in non-linearities between inflows and outflows. In linear systems, a small change in input results in a proportionate change in output. In our non-linear port example, a small increase in the inflow of ships may have no effect on port throughput if there is plenty of on-site container space. But the same minor increase could cause a large backup in a differently configured port. Any chokepoint may cause cascading chokes up and down the system, further reducing efficiency and increasing the backlog. Moreover, once the system is backlogged, it can be difficult to identify the original source of the problem.
Problem-Solving, Feedback Loops, and Government Intervention
The Biden administration has taken several actions intended to help solve the port congestion problem and/or prevent future disruptions, including establishing a Supply Chain Disruptions Task Force, pressing port managers to temporarily adopt 24/7 operating schedules, supporting funding for port renovations in the recent infrastructure bill, and launching a pilot program that may lead to the legal age for interstate truckers being lowered from 21 to 18.
No entity is better suited than the federal government to simultaneously address problems in the ports, trucking, railroads, and warehousing. However, another cornerstone of system dynamics — the concept of feedback loops — helps us understand why government intervention often has negative unintended consequences.
Many of us take a linear approach to problem-solving. We identify a problem, decide on a solution, take action, examine the outcome, and, with luck, declare the problem solved. It is a satisfying approach and one that politicians often feel compelled to take. The combination of public pressure to “do something” and short election cycles make linear problem-solving very appealing to policymakers. Unfortunately, linear problem-solving does not account for the possibility that the problem is actually a symptom of a much larger problem, or that the action being taken may create new unforeseen problems when the system is configured differently.
System dynamics’ closed-loop approach to problem-solving is more nuanced. As we saw in the story of Jay Forrester and General Electric, closed-loop problem solving involves assessing how a problem may be connected to seemingly unrelated issues elsewhere in a system. It also considers the unintended consequences that will ripple throughout the system if the proposed solution is implemented. Its practitioners understand that every action has results that will create future problems that will need to be addressed. The feedback loop never ends. While that approach is unlikely to excite rally goers on the campaign trail, it is usually the best way to solve problems in complex systems like national economies or supply chains.
Perhaps unsurprisingly given the preceding two paragraphs, several well-intentioned federal policies are currently contributing to port congestion. For example, the Foreign Dredge Act of 1906, which was intended to support American shipbuilding by banning foreign built ships from dredging U.S. ports, goes a long way in explaining why so few of our ports are able to handle today’s largest cargo vessels. A lack of capable U.S.-built dredgers has recently limited both maintenance excavation and the deepening of ports, so the ports that are capable of handling massive ships are shouldering a disproportionate share of the congestion burden.
The similarly protectionist Jones Act of 1920 prevents foreign-built ships from transporting goods from one American port to another. By limiting ocean shipping options, the law is placing extra strain on trucking and railroads to handle cargo moving between U.S. ports, thereby reducing the capacity of these modes to haul inland-bound cargo away from overcrowded ports.
Another factor limiting trucks’ ability to haul containers from ports is a chassis shortage. Here, a 2018 tariff intended to make American-built semi-trailers more appealing than their Chinese counterparts helps explain the shortage. The tariff was initially set at 10%, then raised to 25% in 2019, then increased to a final duty rate of 221% in May 2021.
Finally, we previously noted that the recent Infrastructure Investment and Jobs Act includes funding for port renovations. However, it forbids spending the funds on automation, so it will not help address one of our ports’ biggest shortcomings.
Conclusion
The port backlogs will not be cleared overnight. Forrester’s insights explain why: nonlinearities, feedback loops, and path dependence interacted to cause the pile-up in the first place. It is important for government and business not to exacerbate the issue by over-reacting to the problem in its magnified current state, as this can cause its own bullwhip effect. Instead, they should focus on identifying and widening key choke points while eliminating regulatory restrictions that cause needless friction. Small changes can have large consequences, so a light touch may succeed where heavy-handed intervention would risk making things worse.